HOW IS 3D PRINTING HELPING THE WORLD GO GREEN?
October 28, 2021
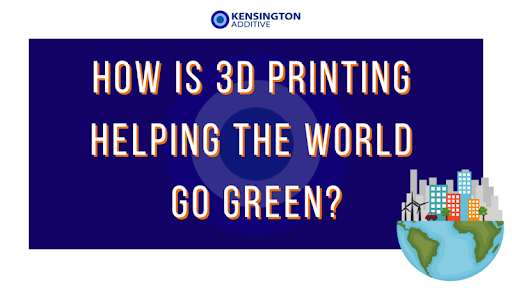
How is 3D printing helping the world go green?
Additive manufacturing is an industry born from the desire to do things differently. Invention, innovation, and evolution were always at the heart of all the advancements in 3D printing technology over the past 40 years.
Throughout its history, the AM industry has battled to establish itself as a viable alternative to traditional manufacturing methods, such as CNC machining and injection moulding. As a result, the focus has always been on developing AM processes to compete in terms of speed and production quality.
Now that AM has proved itself and become a typical process in many industries, it faces a new challenge–how to become more sustainable.
Sustainability is the topic that’s gained the most attention in recent times, and the drive to reduce carbon emissions to net-zero is an aim of many organisations. But, ultimately, this desire is driven by customers who are becoming more informed and aware of the carbon footprint of the products they consume.
How sustainable is additive manufacturing currently?
Inherently, AM is a less wasteful process than other manufacturing methods. Depending on the part being printed, it can use 100% of the inputted material, unlike a subtractive process like CNC machining, which may only use 50% of the original material.
Combine that with topology optimisation software to improve the weight and shape of a part, and redesign multiple parts to be printed as one assembly, and you can save mountains of waste, weight, and processing time.
Producing lightweight parts is crucial for improving fuel economy in all forms of transport. Indeed, the aerospace and automotive industries have embraced AM technology for that very reason. So AM is indirectly responsible for reducing CO2 emissions from vehicles.
However, AM isn’t an utterly waste-free process. Failed prints are one source of waste, although as software and hardware evolve, those should become less of an issue. Another form of waste is in the support structures used while creating the printed part. After printing, the supports need removing and are usually disposed of as unrecycled scrap. While the volume of this scrap is low, it is still a factor to consider.
Metal powders
AM processes like powder bed fusion are worthy of separate consideration as there is a great deal of debate about the powder used. Specifically the unused powder and whether it can be reused for multiple production runs.
When a production run is complete, some of the metal powder will remain untouched. Numerous studies have shown that, with the correct sieving process in place, there is little effect on the properties of the powder, so it can be mixed with fresh powder indefinitely. However, some companies will still scrap off unused powder unnecessarily.
There is scope for companies that use subtractive CNC machining technology to turn the removed material into usable powder for PBF machines, creating a circular flow around their business. A such, that’s one area of focus for companies wanting to make lower their overall carbon footprint to consider.
Plastics
Plastics have become a dirty word in the context of sustainability. And they are indeed responsible for vast amounts of contamination in our oceans.
Again, this is an area that AM technology can lead the way as recycled plastics can be converted into raw material for many 3D printing applications.
For example, Adidas launched a 3D printed trainer made from 95% recycled ocean plastic and sold over a million pairs in 2017.
Construction
One area where AM has made a significant green impact is in the building and construction sector. Using onsite 3D printers and specially formulated low-CO2 concrete, housebuilders can create entire housing estates utilising a fraction of the resources usually involved.
Traditionally, a considerable amount of transport is involved in construction, bringing materials and sub-assemblies to the site. Often those sub-assemblies are over-engineered to help them withstand damage in transit. Onsite printing means the parts can be created as strong as they need to be without this over-engineering. And much of the transport is removed from the project.
Food
Food production is a fascinating application for AM technology, with the potential for 3D printed steak now a reality.
We all know that the meat industry contributes a considerable amount to the global CO2 levels, so replacing traditional cattle-based meat with a 3D printed version could have a massive impact on the climate crisis.
But it isn’t only the replacement of cattle. It’s all the transport and energy that goes into moving live and processed cattle around countries. Onsite printing removes the need for all of the supply chains currently using resources.
In this world, the Israel-based Redefine Meat company seems to be making great strides with its products now used in Michelin-starred restaurants.
Summary
So when looking at the sustainability of AM, it’s clear that a like-for-like comparison with traditional methods only gives a part of the whole picture.
To understand it fully, it’s vital to consider the full life-cycle analysis of the process. For example, what is the supply chain of the raw materials from mining to processing to transport? Also, when viewing it locally, AM may use more electricity than a process like CNC machining. But then you have to consider how that electricity is generated, which varies significantly by country.
So, as with most things, the answer to how sustainable is 3D printing is that it depends on many factors.
However, AM is in a unique position within the manufacturing industry as it is the technology with the most potential to create closed-loop, green manufacturing.
It all comes down to consumer demand. If buyers insist on manufacturers using sustainable methods, the industry will respond and innovate, as it always has done.
Related news
Join our newsletter
Sign up to discover the latest jobs, market insights, blogs and more
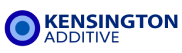
All content copyrighted Kensington Additive © All rights reserved